

.png?width=512&height=512&name=Frame%20(10).png)
Have Questions?
Our MicroGenius® 2 experts are here to help.
MicroGenius® 2
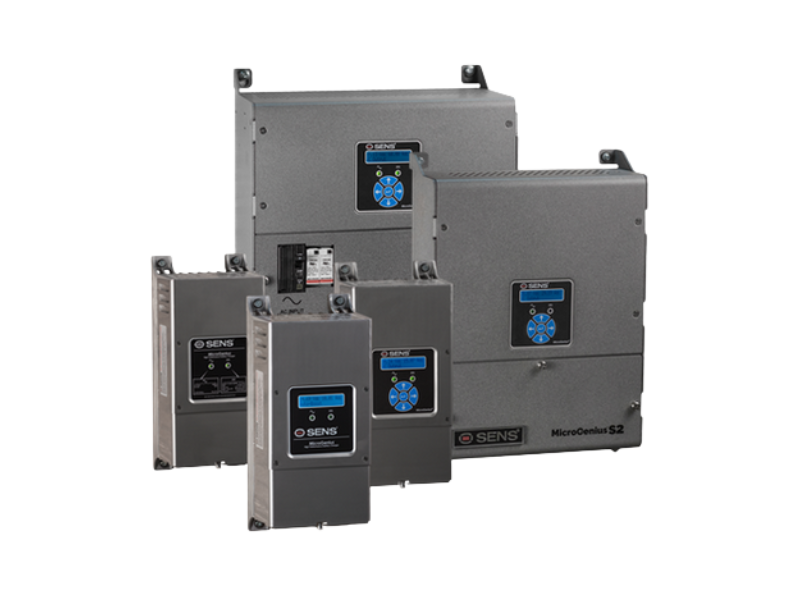
MicroGenius® 2 is a battery charger from SENS that combines the legendary reliability of SENS' NRG with advanced charging, featuring an all-new battery life-extending technology. The small, rugged package is ideal for power generation and reserve power.
Smaller, lighter, more powerful, and charging performance far superior to prior generation products, versions of the MicroGenius® 2 family are ideal for industrial reserve power, marine, and genset engine start applications. At the core of each product is the powerful and rugged MicroGenius® 2 charger/rectifier.
More Power, Less Space
6 to 60 Amps @ 12 & 24 volts in rugged, small housings
Reliable Everywhere
Hardened powertrain & packages withstand the toughest duty
Smarter Charging
SENS: Dynamic Boost and HELIX technologies made available to older technology batteries
Easy Everything
Simple and easy to order, install, reconfigure, and use
Agency Approvals
C-UL, ABS, IBC Seismic, CE, CEC Efficiency, NFPA
Networking Included
Modbus, J1939, parallel operation all standard
MicroGenius2
- How it Works
- Easy Everything
Small, Rugged, Powerful, Innovative
MicroGenius® 2 battery chargers combine the most advanced technology ever applied in their product class with SENS’ widely acknowledged expertise in designing and building the industry’s highest quality, most reliable products.
More Power, Less Space
MicroGenius® 2 chargers employ an advanced high-frequency power converter controlled by a powerful digital signal processor (DSP). This converter delivers up to 50% more power in one-quarter the volume and at 1/8th the weight of previous generation products. Its smaller, lightweight package makes transportation and handling easier, increases the choice of installation locations, and helps reduce costs. With a power output of up to 15 amps at either 12 or 24 volts, the MicroGenius® 450 enables customers to keep up with the ever-increasing demand for more DC power on gensets and workboats.
Other small and lightweight chargers are available, but no others offer the combination of advanced charging technology, ruggedness, and user features of the MicroGenius® 2.
Reliable Everywhere
MicroGenius® 2 chargers are built for tough genset and marine duty. The rugged die-cast chassis provides reliable convection cooling in hot environments — no fans to fail or pump dirt into the charger. And since the MicroGenius® 2 operates at higher efficiency than competitive units (93% peak efficiency, <3 watts in Eco-Float mode), there’s less waste heat to dissipate.
Enclosed models feature a rainproof (IP22 / NEMA 3R) enclosure that doesn’t require a drip shield for protection from rain or dripping water. Conformal coating on circuit boards prevents damage in high humidity, salt fog, or other corrosive environments.
In addition to temperature extremes and moisture, genset and marine environments pose other challenges. Vibration, electrical transients, and general exposure to abuse also make life tough for electronics. But the hardened power train and robust packaging of the MicroGenius® 2 are designed and tested to withstand these challenges. SENS’ Lean production system ensures we build this quality into each and every unit.
Smarter Charging
Weak or dead batteries are the #1 cause of genset failures. Proper charging of batteries is critical to maintaining the health of batteries, and the MicroGenius® 2 does this job better than any other charger available. The reasons are two technologies invented by SENS: Dynamic Boost and HELIX.
Dynamic Boost charges batteries faster and more completely than other charging approaches with a much lower risk of overcharging and damaged batteries. Every time Dynamic Boost engages, it automatically adjusts the charge profile based on current conditions — battery depth of discharge, DC loads, battery capacity, and other real-world variables — to achieve optimal charging. In contrast, most competitors use simple boost timers to keep the charger output at an elevated voltage for a fixed period that is inevitably either too short or too long to achieve a correct charge.
HELIX (High Efficiency LIfe eXtending) technology saves batteries and energy in genset engine starting applications. Today, lead-acid starting batteries used in gensets are replaced nearly twice as often as identical batteries used for vehicle starting, and too often fail catastrophically instead of gradually as they do in vehicles. The reason is that lead-acid starting batteries were optimized for the charging cycles experienced in vehicles. By emulating vehicle charging, HELIX extends the life of starting batteries and reduces the risk of catastrophic end-of-life battery failure. HELIX also reduces energy use by employing a special Eco-float mode when batteries are fully charged and on standby. A periodic HELIX refresh charge tops up batteries at the correct interval.
MicroGenius® 2 chargers contain important other “smart” technologies, such as the ability to recognize and automatically recharge a dead battery, soft configuration of alarm relays to conform to special user requirements, and standard Modbus networking.
Easy Ordering
SENS’ advanced production system configures each charger model to the exact charging profile and settings you specify. All models are 12 or 24-volt field selectable.
Easy to Install
Universal AC input, pluggable alarm connections, and sturdy power connectors make installation a snap.
Easy to Reconfigure
Field changes are easy. Easily accessible jumpers or the optional keypad enable changes to DC voltage, battery type, and float and boost settings.
Easy to Use
Automatically uses the best charging profile for selected battery type. LEDs and an optional display provide an easy-to-understand status.
Frequently Asked Questions
Released in 2016, MicroGenius 2 is an advanced technology industrial battery charger employing switchmode power conversion technology
Any 12 or 24 volt DC-powered mission-critical application, such as marine workboats, power switchgear, engine starting and DC-powered control systems.
MicroGenius2 excels at recharging VRLA, AGM, flooded lead-acid or nickel-cadmium types of batteries. It is also capable of charging lithium batteries with an appropriate battery management system.
Lithium batteries typically integrate protection electronics into the battery to minimize the risk of catastrophic battery failure due to overcharging or cell imbalances. A battery BMS typically coordinates the operation of the charger with the battery. There are presently no standards regarding lithium BMS. Because each one is different please contact SENS sales at 303-678-7500, to discuss integration with your intended lithium battery.
Like other industrial chargers, MicroGenius 2 is designed to power critical equipment and recharge and maintain associated stationary batteries. Applications include electrical switchgear, SCADA systems, marine, engine starting, and related infrastructure equipment. These applications demand highly reliable power conversion, and frequently subject the charger to extremes of temperature, humidity, vibration, and electrical transients. MicroGenius 2 was designed and thoroughly tested to survive these environmental abuses.
Compared with other industrial chargers, MicroGenius 2 delivers a lower total cost of ownership by delivering three key benefits:
- More power in less space – enables installation nearly anywhere
- Smarter charging – reduces the risk of application failure
- Class-leading energy efficiency – cuts operating expense
High-frequency switchmode power conversion enables MicroGenius 2 to deliver the same power as conventional industrial chargers, at about 80% less weight and volume. Together with the charger’s standard NEMA 3R rating, its small size enables the charger to be installed in places that were never an option for competing products. Switchmode technology also guarantees completely silent operation. No more transformer hum.
MicroGenius 2 offers excellent voltage regulation, and battery temperature compensation is standard. In addition, the charger implements advanced charging algorithms that revolutionize the charging of conventional batteries:
- SENS’ patented Dynamic Boost™ system enables MicroGenius 2 to charge batteries faster and more completely than similarly rated conventional chargers, but with a significantly lower risk of overcharge. During each discharge and recharge cycle, Dynamic Boost computes the optimal time to spend in the boost (fast) charging mode. This advanced system modifies charging in response to varying battery size, depth of discharge, battery condition, and size of the connected DC load – all automatically. Batteries receive the optimal fast charge, but without overcharging. Dynamic Boost is superior to simple boost timers or manually initiated boost schemes.
- HELIX™ technology significantly increases the life of batteries in engine starting applications and cuts the risk of sudden battery failure. When charged with conventional stationary chargers, SLI (starting, lighting, ignition) type batteries typically last about half as long as in-vehicle applications. Sometimes these batteries fail catastrophically. HELIX technology significantly reduces the risks of both early battery failure and catastrophic battery failure at end of life. It does this by emulating the charging cycle for which these batteries are optimized, vehicle starting. These improvements deliver improved application reliability and user safety in applications employing SLI batteries.
Regulations and cost savings. SENS MicroGenius 2 is one of the few industrial chargers to meet the demanding California Energy Commission (CEC) appliance efficiency standards, required for all chargers sold in California and Oregon as of January 2017. Operating at peak efficiency of 93% and using less than 3 watts when in standby mode, MicroGenius 2 saves enough power compared to conventional chargers over a typical product lifetime to pay for itself. The high-efficiency operation also allows reliable convection cooling in contrast to some competing products that depend on failure-prone fans for cooling.
Typical 24-volt DC legacy chargers are 70% to 83% efficient. MicroGenius 2 chargers are 91-93% efficient over a broad range of output power. For a charger delivering continuous 200W output, the annual savings of increasing efficiency from 75% to 91% would be 412 KWH/year. Cost savings per year for electricity priced at $0.15/KWh would be $62. The $620 savings over ten years means that the charger roughly pays for itself just in terms of reduced electricity cost.
This symbol shows that the charger is listed in the California Energy Commission appliance efficiency database and that it’s legal for sale in California and Oregon.
Yes. The MicroGenius 2 remote panel contains a display, keypad, and alarm relays. It can monitor and control up to 4 MicroGenius 2 chargers. A network cable with RJ-45 connectors is all that’s required to connect the remote panel. Contact your SENS rep or SENS sales for more information.
Critical applications are frequently in unprotected environments and exposed to extreme temperatures, vibration, dirt, electrical transients, and other threats. SENS employs a combination of robust design and highly automated production that is the most effective way to create industrial products of outstanding quality at highly competitive prices:
To maximize the probability that MicroGenius 2 survives these threats SENS employs thorough “worst-case” design analysis (WCA) and extensive testing. Although WCA is costly and time-consuming, this technique is the only way to assure that components remain free of over-stress at the worst combination of environmental stress, operating limits, and component tolerances.
High-quality production of the validated design is assured in three ways:
- Exercising stringent control over incoming materials
- Employing precise, high-volume tooling
- Making maximum use of computer-controlled production, test, and burn-in systems that help drive down human-caused variation
The quality of firmware and software is critical to all digitally controlled devices such as the MicroGenius 2. SENS employs a best-practice engineering approach called “regression analysis” to validate software quality. At SENS, regression analysis includes extensive software testing of all charger and communications functions against a documented procedure at every release. The rate of software errors, or “bugs”, is logged and charted over time. New software is withheld from release until it clearly demonstrates high-quality release-level stability.
Government regulations on electrical equipment are ever-increasing. Because MicroGenius 2 passes multiple relevant North American and international standards for multiple applications specifying this charger reduces the risk of running afoul of regulators. Standards include:
- C-UL listed for the United States and Canada to multiple UL categories, including:
- BBGQ for industrial reserve power
- BBHH for emergency generators
- QWIR for diesel fire pumps
- BBJY for marine applications (pending)
- Canadian standard CSA 22.2, No. 107.2
-‘Rain Proof’ tested and rated by UL
- CE marked to European directives for Low Voltage, EMC and RoHS. MicroGenius 2 is validated to the more stressful “industrial” test of electromagnetic immunity
- ABS type approved and USCG certified for shipboard and offshore use
- FCC Part 15, Class B certified electromagnetically quiet
- IBC certified for installation in seismically active areas
In addition to complying with minimum statutory regulations, SENS performs electrical surge, vibration and water ingress tests to high levels of other relevant standards applicable to the many applications for which the charger is suited.
Yes. MicroGenius 2 chargers comply with UL 1236, SB13.2, and USCG CFR 183.410 for ignition protection in normally non-hazardous environments.
No, per Section 1705A.13.3.1 of the 2016 California Building Code, equipment and components weighing not more than 50 lbs. and supported directly on structures are exempt from OSHPD approval. Since all MicroGenius 2 models weigh 6 lbs. or less, OSPD approval isn’t required.
Yes. The MicroGenius 2 has a fully filtered DC output with fast dynamic response times and will meet or exceed the performance of most commercial power supplies. DC output ripple is less than 30mV rms, line/load regulation is less than 0.5%, and large transient voltage response (5% to 90% load) is less than 15% with full recovery in less than 5ms. The MicroGenius 2 delivers this high level of performance both off and on-battery.
MicroGenius2 includes two different battery health monitoring systems, each functioning differently and suited for different applications. These are integrated into the charger’s firmware and user interface control.
Battery check is suited for reserve power applications where the charger normally provides DC to drive a connected load. Examples include SCADA and telecommunication systems. Battery check is available on models equipped with a keypad.
Crank Analyzer is suited for applications where there is typically little to no continuous load, and where intermittent loads are large compared with the charger’s output current. Examples include genset starting and electrical switchgear.
Both Battery Check and Crank Analyzer are intended as a general early warning of possible battery problems, giving a simple PASS/FAIL indication of battery status. Their purpose is to summon a trained battery technician to the site for further investigation and corrective action.
Each of these systems observes the battery’s performance when stressed by the actual load, and alerts of a weakening or weakened battery. Because battery performance typically deteriorates prior to complete failure these systems can alert users to the need for battery replacement in advance of actual application failure.
These systems are fully integrated into the charger. They operate automatically. They require no separate hardware, wiring, software or expense. In contrast to standalone battery monitors employing discrete hardware, both systems make use of the charger’s power supply, onboard processor, and high-accuracy digital-to-analog (DAC) and analog-to-digital (ADC) converters.
Some standalone battery monitors are able to provide detailed, trended cell-level diagnostics that reduce troubleshooting time. While valuable on large UPS systems that sometimes include hundreds of cells, these systems require costly hardware, complex cabling to each battery jar, and specially trained technicians to operate. They typically cost thousands of dollars. Even after installation, the complexity of some standalone monitors causes some users to give up using them.
Battery Check assesses whether the battery is capable of powering a continuous DC load drawing less current than the charger’s rated current. It is thus well suited for reserve power applications such as SCADA equipment or communications gear.
Initiated either manually or on a user-adjustable automatic schedule, Battery Check reduces the charger output voltage to a level at which a healthy battery would support the load. During the check, the charger stays active as a DC power “backstop” to prevent the dropping of the critical load in case of a missing or failed battery.
At the conclusion of a successful Battery Check the charger resumes normal operation. When the charger detects a Battery Check failure two things happen: The check is terminated and the charger returns to its charge mode prior to the check, and a latching visual and remote alarm is issued. The visual and remote indications persist until a successful check (of a new battery) or until manually reset.
Crank Analyzer is well suited to assessing the performance of batteries in short-duration high-load applications, such as engine starting or electrical switchgear actuator operation. In each of these applications, the load greatly exceeds the charger’s output current limit.
When a battery discharge meets certain criteria pre-programmed into the charger’s firmware, Crank Analyzer writes a high-speed record of the discharge. If voltage during the discharge drops below an adjustable threshold the charger issues a latching alarm. Regardless of whether a failure alarm is issued, the most recent four records are retained in the charger’s non-volatile memory. The data on these discharges are extracted from the charger in graphical format using SENS PC-based MicroGenius Setup Utility.
Yes. All parameters are adjustable, including whether either warning system is enabled. Battery check is further adjustable for either automatic or manual function, duration of test, frequency of automatic test, and test voltage setpoint. The alarm trigger voltage of both tests is also adjustable.
Battery Check gives the highest accuracy results in a DC system with a relatively large constant load, in general, greater than 10% of the charger’s rated output current.
Crank Analyzer gives the best results on an intermittent load drawing more than the charger’s ampere rating. There is no requirement for a continuous DC load.
- Parallel operation: Two chargers are connected in parallel to the same battery.
- Load share: The degree to which current is shared between two chargers connected to a common DC bus. In theory, two chargers delivering exactly the same output voltage through DC leads of exactly the same resistance will share the load equally.
- Forced load share: A scheme intended to cause chargers to share output current despite normal manufacturing tolerance and unavoidable variation in resistance of charger output cabling
The MicroGenius 2’s digital load share system differs from conventional forced load share schemes in three main ways:
- Connecting the MicroGenius2 load share cable automatically propagates every charger adjustment parameter from one unit to the other. A maximum of 32 chargers can be connected in parallel on the same load share bus.
- Two or more MicroGenius 2 chargers connected in parallel act as one. Selecting a different charging mode for one charger causes the other to also change mode at the same time.
- The optional battery remote temperature compensation probe delivers the same temperature data to each charger to insure the commonality of operation.
In addition, the operation of the MicroGenius 2 digital load share scheme is completely independent of the AC source, meaning that two chargers powered by different grids or from different input voltages will reliably load share.
Digital load share is activated by connecting a standard RJ45-terminated network cable between two chargers using the standard SENSbus port in each charger. When both chargers are powered one charger becomes “master” and the other “slave”. The master charger determines voltage settings and timing of charger operations such as entry into and exit from boost mode. Multiple chargers may be connected in parallel. Should the master malfunction another charger automatically takes over as master.
Yes. Any MicroGenius 2 chargers with the same rated output voltage can be paralleled. Load currents will share according to the percent of rated charger output.
No. Forced load share should only be used when two chargers operate in parallel on the SAME battery.
Batteries are chemical devices whose properties change dramatically with temperature. One of the necessary changes is that the charging voltage must be reduced when the battery is warm or hot and increased when the battery is cool or cold. All battery manufacturers recommend such temperature compensation.
Locating a temperature sensor in the battery charger is a simple, convenient, and inexpensive way to temperature-compensate the voltage output of the charger. When the battery and charger are co-located in the same ambient environment a charger-mounted sensor can give a good approximation of the correct charging voltage. MicroGenius 2 comes standard with an onboard temperature sensor and has dedicated terminals for a remote temperature sensor.
Sometimes, batteries are located in areas of very different temperatures from the charger. In other cases, battery heaters are employed as a countermeasure against battery performance degradation in particularly cold climates. In these instances, remote battery temperature compensation is essential to insuring that the charger delivers the correct charging voltage.
Remote temperature compensation simply extends the charger’s temperature-sensing system out to the battery.
SENS recommends fixing the remote probe directly to the battery, instead of sensing ambient air near the battery. This is particularly important when battery heaters or other temperature-controlling elements are used with the battery.
On battery systems where one polarity is connected to earth ground, we recommend connecting the remote probe directly to the grounded terminal. On floating, or ungrounded, battery systems we recommend fixing the temperature probe to the battery case itself.
Both methods are explained in detail in the installation instructions accompanying the remote probe.
The DC fuse is present to protect against internal component faults. If another component in the charger fails, the fuse will blow if necessary to prevent excessive current output. Such a failure, while unlikely, would require the charger to be repaired anyway.
Unlike legacy chargers with replaceable fuses, the MicroGenius 2’s output fuse is unlikely to ever blow from an external cause. The reason is that the charger employs an exceptionally fast control system. It’s so fast that it can easily disconnect or electronically current limit an energized charger in nearly all cases where over-current protection is required, such as a reverse-connected battery or shorted output leads.
Legacy chargers that operate at line frequency (50- 60Hz) have control systems that are too slow to react immediately to over-current-inducing events. The MicroGenius 2, operating at greater than 100,000 Hz, easily responds fast enough.
While it is still possible to blow the output fuse in the case of a lightning strike or other huge DC transient, any such event will most likely damage other components in addition to blowing the fuse.
Given all these factors, SENS elected to solder in the fuse for increased reliability.
SENS designed the MicroGenius S2 and S4 using the same engineering approach — design rules, conservative component selection, worst-case analysis, circuit simulation, environmental testing, shock & vibration testing — that we used with the SENS NRG and IQ models, both of which are exhibiting observed MTBF in excess of 1 million hours. (Observed MTBF = total hours in operation/number of product failures). Given that the S2 and S4 are new products, we would conservatively project MTBF well in excess of 250,000 hours for both.
have questions or need help?
The SENS team is here to help. If you have questions or need help, reach out and start a conversation.