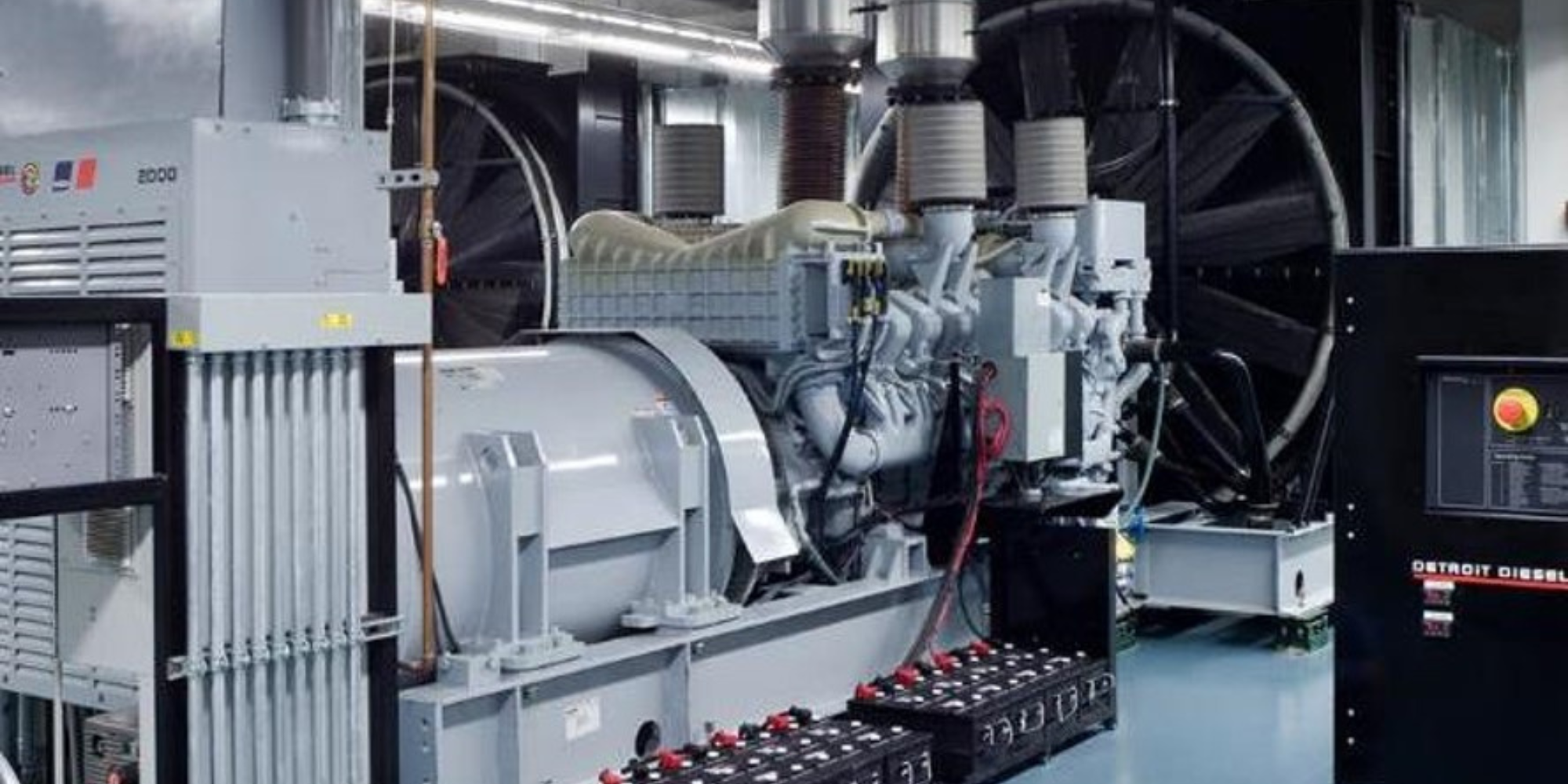
How a factory‑assembled system simplifies mission critical engine starting and boosts reliability.
What happens when a mission critical facility experiences a primary power fault?
Let’s examine that sequence:
- The primary power source to a mission critical facility suddenly faults.
- The ATS senses the fault and initiates the generator start signal.
- Meanwhile, critical operations are now running on short-term battery power.
- The standby generator receives the start signal, and issues start commands to its starting system.
- Starter solenoids engage, and the engine starter motors activate.
- The starting battery cables suddenly twitch as thousands of amps of current begin flowing from the batteries to the starters.
- The giant engine crankshaft, AC alternator, and radiator fan begin spinning.
- Faster and faster the engine turns until the engine starts.
- The engine roars to life as its 16 massive cylinders fire in motion driving 3MW of backup power to the mission critical facility.
- The facility breathes a sigh of relief knowing its operations will safely continue until the primary grid fault is corrected.
This is why mission critical standby power generators are equipped with DC redundancy, to ensure that even in the case of component failure, the standby generator starts - every. single. time.
But getting there has been far from straightforward. Behind every reliable engine starting system design lies a tangle of components.
A typical mission critical DC starting system requires specification, procurement, and installation of the following:
-
4-12 heavy-duty lead-acid starting batteries
-
Battery racks
-
1, 2, 3 or 4 battery chargers per engine
-
DC disconnects
-
Best battery selectors
-
Cabling, conduit, and terminations
-
Communication and monitoring systems
This has led to complicated systems, long installation times, and crowded generator enclosures. Additionally, traditional lead-acid battery systems have a very short life, requiring frequent replacement and regular maintenance. The onsite complexity of the DC system adds further reliability and operational risk.
Caterpillar and Cummins have long stated that the number one cause of standby generator failure is the starting battery system.
But there is a revolutionary new system addressing these challenges. In January 2025 SENS introduced the SuperTorque 8ZR - a fully integrated, factory packaged engine starting system.
Instead of specifying, sourcing, and installing dozens of components, engineers and operators can now rely on a single, compact, engineered system. By moving to the all-in-one SuperTorque 8ZR, companies now eliminate dozens of failure points with a single stroke.
Factory-packaged starting systems bring quality and consistency that’s hard to achieve with individually assembled setups. By significantly reducing the number of on-site connections and manual integration steps, they minimize the chances of installation errors and early-life failures - resulting in a system that’s ready to perform reliably from day one and over the long term.
The SuperTorque 8ZR comes standard with a factory 10-year full replacement warranty and is designed for a 15-year service life.
Revolutionary Space Savings
The SuperTorque 8ZR radically changes the generator enclosure by cutting the space required for the DC system by 90%.
The SuperTorque 8ZR Architecture
The SuperTorque 8ZR is a single solution that arrives ready for simple installation. This integrated system comes pre-wired, preassembled, and factory tested as one unit. One part number from SENS delivers everything you need for your complete engine starting power system.
“The 8ZR provides the entire DC power system for mission critical engines - in a single part number, configured to your engine, redundancy, and space requirements.”
- Eric Solanyk, Genset Power Solutions Director
Key features of the 8Z Rack include a steel cabinet housing high-performance NiZn battery modules, an embedded smart charger, built-in control electronics for battery management, built in redundancy for engine starting, alternator, and engine control power, and DC disconnects.
It’s engineered as one unit, UL-listed and seismic-certified, so you know it meets all safety standards out of the box. Simply bolt the 8Z Rack into place and connect it to your generator and AC supply - a drop-in installation.
Engineers, procurement teams and facility operators are choosing the 8Z Rack because it increases reliability, removes risk, saves space, and reduces costs:
- Simplifies sourcing: one part number replaces dozens of components
- Frees up space: 1/10th the space of traditional systems.
- Reduces risk: better battery technology, better packaging
- Speeds up installation: saves ~8 hours compared to piecemeal setups
- Lowers long-term cost: NiZn batteries last 15 years and require no maintenance
- Improves sustainability: 96% lower lifetime GHG emissions vs. lead-acid systems
The 8Z Rack is the new way engine starting systems get designed, purchased, and installed.
For mission-critical operations, an integrated system is better
Whether you’re running data center operations, managing power systems in healthcare, or overseeing remote sites for energy and communications - reliability and speed matter. The SuperTorque 8ZR gives you both and is shipping at scale to mission critical facilities today.
Want to see how the SuperTorque 8ZR fits in your application?