.png?width=576&height=512&name=Frame%20(9).png)
Have Questions?
Our DC PowerRack™ experts are here to help.
DC PowerRack™ Relay Rack System
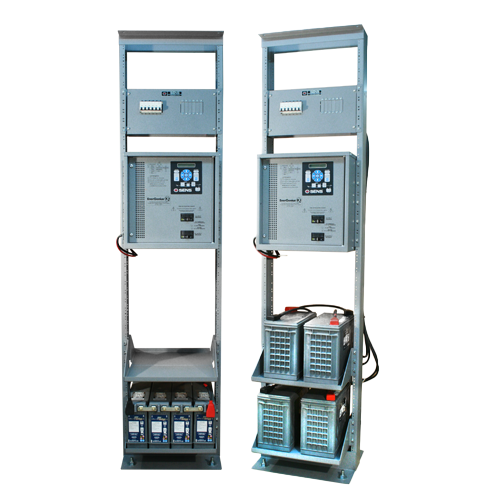
SENS DC PowerRack™ is a complete DC power system in a 19″ relay, factory-integrated and ready to install. Because SENS PowerRack ships assembled*, it can radically cut DC system installation time, cost, and risk. It is suitable for virtually any indoor application or load requiring non-stop DC power up to 48 volts DC.
*batteries ship strapped to system pallet for installation on site.
Complete Non-Stop DC Power System
- Includes battery charger, battery, DC distribution
- Sturdy powder-coated 19″ EIA steel rack
- 12, 24 & 48 volt systems with front or top terminal batteries
- Optional battery string breakers, sinewave inverter
- Configured to customer requirements, yet ships pre-assembled
- Single source convenience
DC PowerRack™ Relay Rack System Applications
- Critical process control power, ideal for control buildings at well-head pads & pipeline stations
- 48 volt switchgear applications
- Communications
have questions or need help?
The SENS team is here to help. If you have questions or need help, reach out and start a conversation.